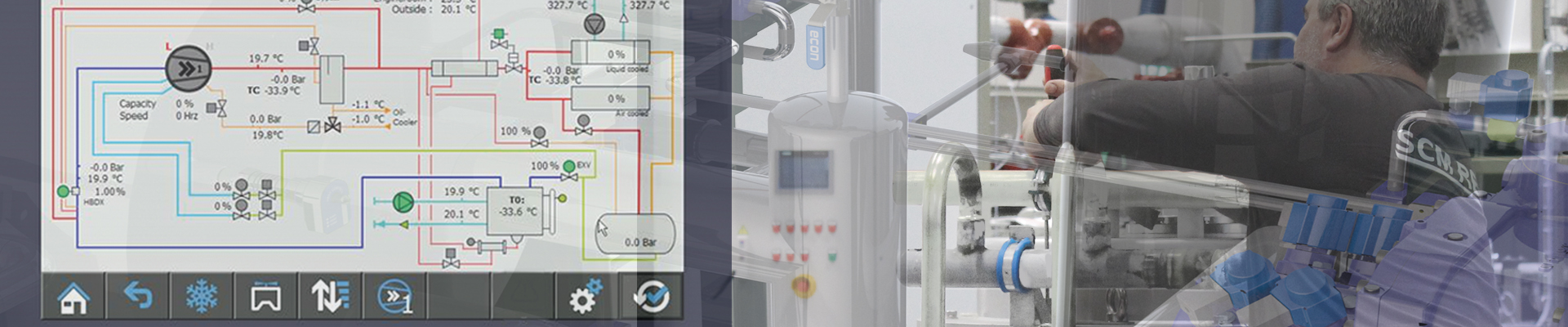
Safety & maintenance
The chillers design is compact with a hermetically factory welded closed circuit. The leakage from shaft seal being eliminated completely by using semi-hermetic compressor.
Dedicated Siemens S7 software can regulate by itself without human intervene during normal situation. Multiple safety prevention mechanisms are already tested and built in to sustain operation in difficult situations and prevent damage in emergency. Such as the fail safe pump down function against blow-out of ammonia.
Safety features
HP and LP pressure switches are installed as standard. Dual safety relief valves are welded on each pressure vessel. The optional safety relief valves are connected to one common relief pipe.
Ammonia detector and alarm are built into all chiller models and powered by independent supply. To help our customers comply with different local legislation, the detection level can be adjusted. The sensors are pre calibrated over the full range.
The temperature and humidity inside the electrical switch box is monitored and controlled to minimize the environmental influence and work in a wide temperature range from -5 up to 40°C and 85% relative humidity. For low temperature applications an additional heater is available as an option.
Maintenance features
- SCM REF ammonia chillers are designed to be service friendly. The components are arranged in a well-thought-out way to make sure their accessibility.
- All major components can be isolated by ball valves easily.
- The connecting pipes where oil filters are installed, are designed to be short as possible.
- A hand drain valve is installed at the bottom of evaporator for checking or draining oil.
- For air cooled condensers, each fan is equipped with a service switch
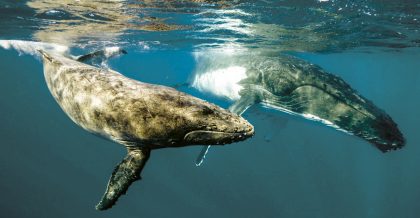