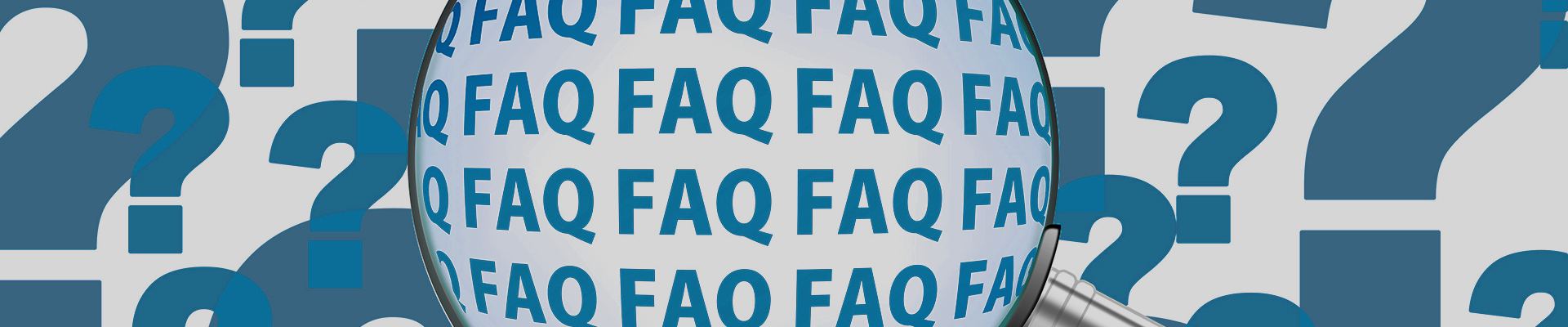
FAQ
Commissioning
How is commissioning supervised?
- SCM Ref offers remote telephone support during the planned commissioning. Because the PLC control is carried out with a 4G router, we can remotely monitor the installation and during commissioning after connecting the voltage.
- The regulation and control of the standard Chiller works fully automatically after setting the desired setpoint. After adjusting the linked hydraulic process by the installing party, the Chiller and the linked processes must be monitored for a few more days to assess whether the installation functions optimally within its area of use and the working conditions
Is a skilled technician required for filling during commissioning?
- For filling the installation with refrigerant and oil, it is a legal requirement that the work be carried out by a skilled and certified technician.
- Before filling with refrigerant, a “pre-commissioning inspection” (KVI) must be carried out on site by an EU Conformity Assessment Body (EU-CBI). (Notified body).
Compressor
Can the Chiller be equipped with an Open type screw compressor?
- The lower half of the capacity range is covered with a series of 6 single Open Bitzer compressors. Due to the available space on the standard frame, there is room for an open screw compressor with an electric motor.
- The compressors with electric motors are installed in such a way that they can be integrated in the same housed Chiller rack.
What are the advantages of a Bitzer compressor?
- The brand has a reputation in the market.
- The electric motor can be easily replaced in case of damage.
What are the advantages of the SRS compressor type?
- The semi-hermetic version has no risk of leakage at the shaft seal.
- It has a built-in permanent magnet electric motor with a compact footprint and up to 30% lower connected load.
- A double compressor in combination with the high/low speed guarantees a redundant design.
Sales
What do I get in return for the investment?
- Everything is in it! The installation work is limited to setting up the installation on location and the water-side and electrical connection.
- The stand is prepared for easy mounting, without extra expensive welding and installation work on site. All welding, NDT examinations, etc. have already been carried out in the workshop.
- The Chiller is fully produced and approved under PED factory type approval of SCM Ref.
- The control cabinet, complete with the control unit, is equipped with pre-programmed templates and clear work instructions. This means that no expensive knowledge is required for programming and supervision.
- Detection, alarms, emergency stop operation, etc. for outside the engine room are fully prepared and standard part of the delivery.
- The electrical control and software are fully dry tested before delivery.
- Design and control are aimed at a “Fail-safe” working operation. As a result, no unnecessary malfunctions and service visits due to failure of the installation.
Heat recovery
The customer wants to use heat recovery. Is that possible?
- The Chiller has the option of high temperature heat recovery on the oil cooler.
Energy performance
Does the Chiller have a high energy performance?
- The high SRM Tec COP values are achieved by a patented rotor profile (5/7) specifically developed for NH3 in combination with the highly efficient permanent magnet motor.
- At full load, the COP can be slightly more favorable for certain open models because there is no heating of the suction gases via the electric motor.
- Each compressor has a high efficiency and wide control range with its own VSD (Variable Speed Drive) of 35 – 100% capacity. Without using the Slider function.
- With the slider function, the capacity per compressor can decrease further by up to 18% without falling into start-stop operation.
Refrigerant circuit, operational reliability
What is the function of the high pressure liquid vessel?
- The receiver functions as a fluctuation receiver for evaporator capacity control and for fail-safe operation with:
- A modulating LP level control based on the heat load in the evaporator.
- An “Overshoot” liquid injection in combination with a hot gas bypass control to prevent the so-called “Dry boiling” in the event of a temporary overload of the evaporator.
- An additional liquid injection when the oil temperature / discharge gas temperature is too high.
Climate, operational reliability
Under which outdoor conditions can the Chiller be used?
- The control box is equipped with controlled ventilation and heating for the working area up to a maximum of 85% RH.
- The working range for the Chiller in the basic version is between -5 °C and 43 °C.
- Optionally with a winter package, this range is reduced to -15 °C.
- The maximum design pressure is 28 Bar (64 °C).
From and up to what temperature does the optional winter controller work? What does that mean?
- Below 0°C, an optional winter package is offered.
- An additional heating element in the control cabinet protects the equipment to a minimum ambient temperature of -15°C.
- A high-pressure compressed gas injection is provided for a minimum pre-pressure on the expansion valve for the evaporator.
Condenser
Standard OEM condenser, what are the advantages?
- The supplied OEM condenser has an integrated oil cooler circuit over the entire heat exchanger surface.
- The integrated oil cooler prevents an additional plate heat exchanger with dry cooler and glycol pump circuit.
- The nest of boiler tubes has been developed with 10 mm stainless steel tubes for a “Low charge” NH3 content.
- Equipped with a central compressed gas header and a welded three-way dual shut-off valve with pressure relieve valves.
- Equipped with two sets of connection flanges per circuit with the “Prefab” connection piping set.
What are the requirements, maximum distance and height of the air-cooled condenser in relation to the Chiller rack?
- For the remote condenser, a maximum total length of 25 meters has been considered, of which 5 meters is discharge line.
Can the Chiller operate on a process where the refrigerant has a variable flow rate?
- Yes, when ordering, the customer must indicate whether the Chiller is designed for a fixed or variable flow rate. This is considered when designing and connecting the evaporator heat exchanger.
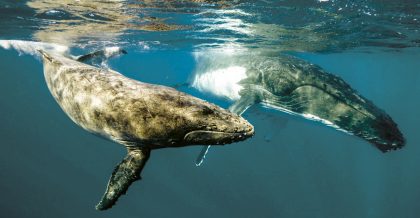